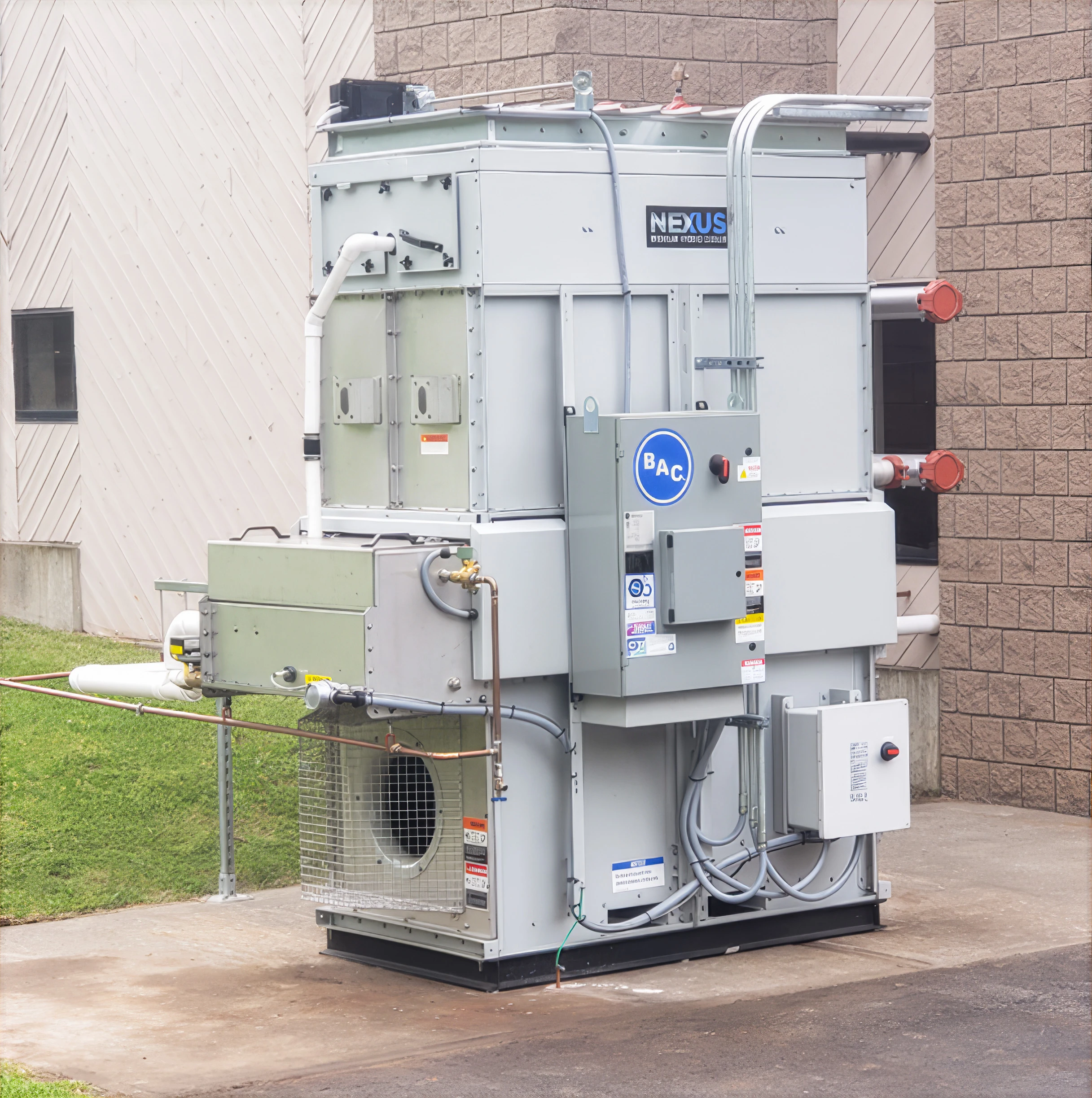
MGM Building
June 18, 2024
Equipment:
BAC Nexus Fluid Cooler
Description:
This project hits particularly close to home for us, as it involved replacing the 35-year-old BAC fluid cooler at our home office in Syracuse, NY. The challenge here was that it put us on both sides of the sale – as both the sales rep and the building owner. While we always take to heart the things that matter most to building owners (installed costs, operating costs, performance, and efficiency), it was a fantastic exercise to actually put ourselves in the shoes of our customers and carefully examine things from that perspective.
The goal was to select the unit that gave the best combination of purchase price, installed costs, and operating costs to maximize our investment. We were excited to find that the answer was a new type of product designed from the ground up – the BAC Nexus Fluid Cooler. What’s surprising was that it was actually the most expensive unit, but the savings over its life in terms of installation, energy, maintenance, and water treatment costs justified this investment for us as owners.
Some info on the unit itself – it uses state of the art components not previously applied to this type of equipment: direct drive plenum fans with EC motors, stainless steel brazed plate heat exchangers, and packaged PLC controls for optimized operation. The heat exchangers are especially noteworthy as they exponentially enhance heat transfer in both wet and dry operating modes when compared to conventional coils. Another noteworthy feature – the unit controller synchronizes the operation of the spray pump and unit fans to optimize energy and water use.
Now to the fun part – just how is an owner going to realize the savings over time? Maintenance costs are reduced in a couple of ways. The first way concerns water treatment requirements; the unit operates with 1/5th of the sump water charge compared to a conventional cooler and allows for the sump water to dump regularly based on conductivity. Small volumes of water are required, which reduces water treatment costs to basic periodic testing required by the state. Second, there are savings with the elimination of fan belts and fan VFDs.
Installation costs are reduced as well; the motor control center and PLC control panel are both installed and wired in the factory – a real time-saver once the unit is on-site and ready for startup.
Residual benefits include significantly reduced fan noise and a much smaller box size. The modular design approach allows for a wide range of capacities, all capable of transport to rooftops in freight elevators. The low sound would allow installation in almost any proximity to operable windows, outdoor seating areas, or property lines.
For these reasons, we felt this the best solution for our building and proudly display the equipment for training and information purposes.
-Chris Miller, President of Modular Comfort Systems